
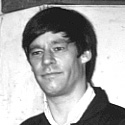 |
Seated next
to an old wood-burning stove, surrounded
by wood, ivory, metal, low and high tech machinery and
pipe parts of every description, Charley Kron, master
pipe maker and Principal of C.E. Kron & Co.
talks about the business of pipe making and the growing
demand for quality drones and chanters in the US. |
Charley, before we get to pipe making, let us first talk about
your piping background. How did you start, your teachers,
etc?
I always had the ambition to play, ever since I heard a Pipe
Band when I was very young but I didn't start until I was
in London as part of a college program. It was June, the semester
was finished and I had an old Pakistani practice chanter my
parents had bought me that I carried around for years and
I thought I would go to Scotland and look for someone to teach
me. Unfortunately my parents were also sold a few pipe reeds
to go with the chanter. Of course I could never get them to
work. I also had a College of Piping Tutor. So, I went up
to Scotland with my chanter, tutor book and two pipe chanter
reeds looking for a teacher. I knew absolutely nothing!
Then what?
Well, I went to Edinburgh, walked in to the J & R Glen
shop and met old Andrew Ross. He looked me over, God knows
what he was thinking, but he hunched over an ancient typewriter
and typed out Pipe Major George Stoddart's address and phone
number for me. He was Pipe Major Gavin Stoddart's father.
I stayed on for three months and took lessons five days a
week from Pipe Major Stoddart. He was retired and had the
time. I remember he loaned me a practice chanter reed when
we first met, after he saw what I had.
How did it go?
I learned a great deal that summer and the next -- three-hour lessons five days a week, followed by eight hours practice each day and on to the pubs around nine at night. I enjoyed going to the Eagle Pipers in the West End Hotel, where many pipers met. I met many of them including Paddy Atkinson, known for escaping from Dunkirk in World War II on the last remaining spot on an overflowing rescue boat. He was told to leave his pipes on the beach and get aboard; he refused, instead he cut the bag off, took the set apart, shoved the sticks in his pockets and jumped in!
When did you actually start on the Pipes?
Well, that's another story. George Stoddart was teaching
a young boy who was already on the pipes. George asked me
if I wanted to try them? I never played before but I picked
them up, got the hang of the mechanics and played The Earl
of Mansfield. I remember the expression on George's face!
My first time and it was my 19th birthday.
When did you get your first set of Pipes?
By that time I had a new practice chanter from Jimmy Tweedie
at Inveran House, and Pipe Major Stoddart said I should get
my Pipes from George Kilgour, who "won't make a bad bagpipe
because I'll hear about it!" That’is how I met
George Kilgour. After the two summers taking lessons in Scotland
I went back for fifteen months of intensive teaching and practice.
I started commuting to Glasgow and taking lessons from Jim
Johnston on Robertson Street. I also took lessons from John
D. Burgess who became a friend of mine and also from Pipe
Major Evan MacRae, formerly of the 1st Battalion Cameron Highlanders,
who became my teacher for many years.
Had you competed in any Solo events here, or in Scotland?
Yes, I did. I usually went to the smaller games in the Highlands. It was great, because more often than not top pipers would show as well; people like John Burgess and Ian McFadyen. I started competing in Grade IV here but never won a prize although I did win prizes in the Open Competition in Scotland! So I moved myself to Grade One, which you could do then, and then to Open and started to win medals!
Did you play with any Bands in the U.S.?
Yes and here’is how that happened: I met my future
wife, Joan, in Scotland; she was an American studying there.
Also living in her apartment building, fortunately for me,
was Bob Costigan, well known to EUSPBA drummers and Pipe Bands.
At the time, Bob was playing with the Monaghan Band and he
invited me to meet Bertie Patterson, the Pipe Major. I joined
the Band around 1981. They were a good group of dedicated
players.
Did you meet any pipe makers when you were studying in Scotland?
Well aside from George Kilgour, as I mentioned, there were Andrew Ross and Jimmy Tweedie.
What was George Kilgour's Pipe Making background?
At the time George was in business for many years. He was
an excellent pipe maker, having apprenticed to James Robertson
and the Robertson line of pipe makers. I believe Willie Sinclair
also apprenticed at Robertson's in the 1920s.
When did it occur to you that you wanted to become a pipe maker as well as a pipe player?
I was always hanging out in George Kilgour's shop. The idea
must have been forming in my mind. The J&R Glen shop was
up for sale, the dollar was strong at the time, and real estate
was very affordable. We talked about buying the shop and setting
up a business. My father and Grandfather were outstanding
machinists with an Old World reverence for quality, precision
and reputation; I suppose it rubbed off.
So how did it happen that you set up your business here on the banks of the Hudson River in New York and not in Edinburgh?
As it turned out it was very difficult for an American to
start a business venture in Scotland so we then talked about
moving the entire operation to the US which we did, in early
1987, as the Kilgour & Kron Corporation. It was unusual
because I owned the business and continued as an apprentice
to George at the same time. George retired in late 1995 and
returned to Scotland. And the firm is now C.E. Kron &
Company. I was lucky to hire Dave Atherton who is a real craftsman
and now a master pipe maker. He’is a major part of our
success.
I imagine it’is not easy to just hang out a sign
and claim to be a pipe maker, an American one at that, given
the impression that Pipes are only made in Scotland.
Passion for the instrument itself and a fanatical attention to the craft makes you "authentic." I had nine years experience with George before he left and a total of almost 15 years at this point. Arguably we are one of the more experienced pipe making brands in business today, here or in Scotland. Our Pipes and our business are now well established in the US. Where you make them is not nearly as important as how you make them.
What is the connection between quality of sound and the making of the pipes, the process? Does one lead to the other?
Yes. First, you start with he wood, we use African Blackwood,
which is the best you can get and the best for making a set
of pipes. Some of the older pipes were made with ebony, going
back eighty to a hundred years ago. Ebony is an excellent
wood, but quite brittle. It does have a mellow tone but that
might be because of the age of the wood in the older ebony
pipes.
What really distinguishes one pipe maker from another, one set of pipes from another?
Knowledge, first; in our case handed down through generations;
secondly, experience, which we certainly have and finally,
the details, the care in making them. That's the difference
between a great set of pipes and an ordinary one. There are
no manuals, and only a very small handful of pipe makers could
ever write one anyway. It’is dedication to the art and
personal pride that will never let us send out a set that
we’are not happy with. At this point I believe we are
more "traditional" than any of our competitors because
we’are not allowing ourselves to be hurried into a "production
line mentality." We’are building our reputation
one chanter, one drone at a time. We’are handcrafting
heirloom instruments and the fact that my name is the last
thing that goes on keeps me very focused on quality.
What then, is a set of Kron Pipes, versus any others?
In the end, it’is fourteen pieces of the finest wood,
worked into a musical instrument, using ancient and modern
techniques that we believe are the best set of pipes you will
ever own. Our wooden chanter, the Medallist, took years to
perfect. It’is been steadily gaining a following as
more advanced pipers add it to their inventory. And don't
forget the sound of the drones, which are the indicators of
craftsmanship. The drones can make or break a reputation,
for maker or player.
Are there any legendary pipe makers that you admire?
Well, yes. David Glen and his pre-world war II firm come
instantly to mind as one that I admire above all. His pipes
were gorgeous, including the post-war sets, not to be confused
with reproductions of those sets. I mention that because the
war took away so many quality pipe makers; many of them chose
not to continue in the craft when they returned. As a result,
there was a tendency for the quality to slip in the post-war
years. The well-established makers could still attract quality
turners but the consistency wasn't there, the elegance and
beauty of the pre-war sets.
How do you know the pipes are just right and you’are
ready to stamp your name on them?
First, you can tell a lot by looking at the set, looking
at the bores, the fit, and the finish. You can look up a bass
drone bottom, for example, and you'll look for smoothness,
evenness. and the absence of the slightest imperfections.
We don't make "good enough" pipes. I make them the
way I learned how, they are either perfect or, as you can
see, they go into this nice wood burning stove here to keep
us warm during the Winter. You learn, you learn more, and
you keep improving.
You've installed some pretty sophisticated equipment
for producing a plastic chanter. Up until now you were primarily
making a wood pipe and chanter? What caused the expansion
to plastic?
Market demand, for the most part, and the fact that competition is going after that market. The demand, of course, is coming from the growth of pipe bands across the country. Our wooden chanter, which we market under the Medallist brand, will remain the choice for solo players and competitors.
What are the keys to success in marketing the new plastic chanters?
Price, quality, availability, the big three, and we intend to be competitive in all areas as we introduce the new chanters.
As a "traditionalist," what do you think of a full set of plastic pipes?
I can understand a market demand, if one exists, for an inexpensive
set of pipes for people who are just not sure about their
level of commitment or their talent or desire. If a good quality,
workable, relatively inexpensive instrument can be made to
meet that requirement then that's fine. In my case, however,
it would be marketed under a different name than mine.
Do you make pipes according to traditional methods, measured against the well-known Scottish brands?
While our design concepts are traditional we use both older,
traditional equipment for our wooden line alongside ultra-modern
machinery for exotic materials. In fact, David Glen made his
pipes on one of our lathes from his shop on Greenside Place
in Edinburgh and we have a lathe once used by Robertson. I
should add that George Kilgour described our American lathes
as ‘the finest ever for making pipes.’Well known’
is just a function of time. Our brand is growing through personal
use and the fact that quality pipers are now starting to use
them in significant competitions.
Would you go out on a limb and comment on the Pipes coming in from Scotland?
Well, not too far, I hope. I can tell you the old-line pipe makers would be upset at the lack of quality in many pipes being sold today, not all. We see it in the pipes that are brought in to us for repair. The care and workmanship is just not there. With the growth of piping in the US and other countries, satisfying demand appears to have moved ahead of quality control. Unfortunately many pipers are just assuming that "a pipe is a pipe" and the pipes are top grade. Guess what? A significant number are not. Concentrate on the fit, the finish. Is the wood and metal threaded, or just glued? Is production relatively limited? Look at the combing and the quality of the wood.
As in any business, brands are perishable. Any well known
brand will fail if it takes the consumer for granted; or worse,
assumes the consumer is ignorant. In this business you can't
hide your brand, unless you give it another name. Every time
a piper strikes up you’are on trial.
Is there a "sound" you are trying to achieve for in your Pipes?
Well, that's like describing a color. Deep, rich, full and
mellow are descriptive words that come to mind. And how they
integrate with the chanter. The overall effect is deeply satisfying
to the serious piper.
You've described your pipes as an "heirloom investment."
What are you suggesting?
Because of the quality, workmanship and sound they will last for generations. With the exception of the all-plastic set for special situations, there really should be no such thing as a "first set of pipes." With the exception of ornamentation, and with proper care, the pipes should last for a lifetime.
You repair pipes, as well.
We do and we’re a bit proud that people are sending us classic pre-war, and even 19th Century pipes, for repairs and rebuilding, since they know we have the technical skill and equipment to match the original in every way, save for the age of the wood. For any repair, we match the original combing and we will even work with exotic woods.
What would someone look for in a new set of Pipes?
First, it would be ideal if you could visit the Pipe maker's
workshop and get a feel for the operation, to see the hand
work and labor involved, and the quality control processes.
I would also say it's important for the pipe maker to have
his own name stamped on the pipes, attesting to his personal
belief and guarantee in the quality.
Are you at capacity now, given that fact that you and your associate Dave Atherton hand-make each set of Pipes?
Business is very good and we are adding some additional capacity.
It's an enormous undertaking and very costly to expand the
line. We've made a large capital investment in new equipment
to produce both plastic and Phenolic chanters.
Phenolic?
It's not the same as plastic. It's Phenolic resin. I'm not
sure if any one else is using it. It's hard to work with but
it makes a very loud and very strong chanter. It's certainly
a leading edge process but it's much harder to manufacture
so we're sorting out where to fit it in the line, from both
a price and performance point of view.
Do you have any pricing advantages since you manufacture in the U.S.?
Not really and here's why. It's a shorter distance from where
the wood grows to Scotland and the wood is heavy so we have
to pay more to cover both shipping distance and weight. But
the impact on our pricing is no more than shipping the finished
set of pipes from Scotland to the U.S.
From a marketing point of view I imagine getting some of the top players to use your pipes is very important. Have you had any success?
There are a handful of very significant players who have
our pipes and chanters and it's just a matter of time, I believe,
before they will allow us to use their names. That may sound
mysterious but it's not meant to be. I'll drop names when
they are using them, and winning of course, in the premier
grade competitions.
Do you see any trends in what pipers are looking for?
Well, it seems that the pitch of the chanter continues to
go higher. I don't think it's too sharp right now but any
higher and it will be. It’is hard to say who is causing
this, the pipe maker or demand from pipers and Pipe Majors.
We do make our plastic chanters a wee bit sharper than the
wood ones because bands tend to want a sharper sound than
do soloists. I remember Seamus MacNeill always complaining
about sharp chanters. Originally, George Kilgour and I made
a flatter chanter, but now we're consistent with trends in
the market.
Speaking as a pipe maker do you have any opinions on reeds?
Oh, yes. There again, the reed makers are part of the trend
towards sharpness and might be leading the trend. However,
any reed maker will want to make his reeds work with a wide
variety of chanters and drones. We buy reeds from many makers
but we ask them to send us "ordinary" reeds, ones
that are not exceptional, just good reeds. Our tolerance for
variation is very low; any chanter that doesn't make the grade
using a variety of reeds is discarded. We're also pretty excited
that Mark Lee, in Oklahoma, has licensed us to be the exclusive
manufacturer and distributor of his new "Rocket Reeds,"
so named because of their very distinctive nose cone design
and the fact that they are made of exotic space age glass
and carbon composites. Mark has redefined and evolved the
paradigm for steadiness and balance. When you strike in the
bag you get instant gratification.
What is the pitch now?
There really is no " right" answer and her's why:
it depends on too many variables. These would include the
type of reed, its strength and the quality of the cane. Is
the reed designed sharp or flat? The construction of the chanter
and type of wood play a part, particularly the smoothness
of the bore. Many bands have a bias toward sharper reeds while,
admittedly a generalization, a lot of solo players prefer
a slightly flatter tone. You also have "dry "and
"wet players," which makes a difference. In fact,
many players today use a "dry system" with non-hide
bags and water trapping enclosures. And, don't forget weather
–playing in Texas on a summer day is a bit different
than in sleet and rain during an early March parade in Boston!
Everything affects pitch. In the end, solo pipers will decide
what pitch is pleasing to them and Pipe Majors will do the
same for bands. Like hemlines, "fashion" plays a
part. You can listen to tapes and records from twenty years
ago and you'll see how pitch has moved around.
How many sets do you make a week?
Together, George Kilgour and I were making one a week, about
forty-eight a year. Now we're making about a hundred a year
but with our new capacity for the plastic chanters we can
greatly improve that. Our new machinery makes a lot of parts,
especially metal ornamentation like ferrules, much better
than by hand. It's not only more accurate and efficient but
it’is certainly faster. Its not just "hand making,"
it’is care and attention, man or machine. Each pipe
is conceived individually and executed with the same care.
Any examples?
Well, you can make an inside thread on a piece of wood by
hand on a lathe and make it perfect. But with silver, if you
cut each ferrule from a tube, put it in the lathe and make
the inside thread by hand it won't be as good as in the automated
machine. The machine will take the entire tube, and cut and
thread each ferrule perfectly because of the exactness, tolerance
and measurement.
How would you describe your business philosophy?
Well, let’us see: the highest quality you can get;
no sacrificing on the integrity of workmanship; traditional
methods; finest wood and ivory. It doesn't matter if our customer
is an eight-year old piper getting his or her first set of
pipes or an Open Grade medal winner, they will get the same
set of pipes. They could stand in front of me and exchange
the pipes between them and it wouldn't matter. Dave and I
will never have to worry about selling a set of pipes that
we're not pleased with. |