
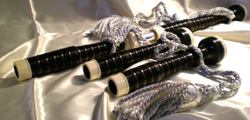
I have decided to revamp and simplify my product line. For
the last eight years CE Kron & Co. has made two models of
bagpipe: the Heritage (a copy of Jim McGillivray’s set of old
Henderson pipes,) and the “Standard”, which is the pipe the
Company has always made. To reduce the cost and complications
of maintaining inventory for these two styles of bore the
Company will now make only the Standard, with a few
modifications. I have used some of the elements of the
Heritage to beef up the sound of the bass drone, and to
strengthen the pipe overall. These modifications do not effect
the ease of setup and the efficiency of the old Standard
model.
I have also simplified the range of styles. The Company now
offers this pipe in the models noted on the
bagpipe gallery page.
The new pipe also looks a bit different, more like older
Edinburgh style pipes. It has a slimmer profile, except on the
tuning pins, which are beefier.
I have arranged it so that I have as much control as possible over
my product. All the parts on my three basic sets are made in my shop.
This gives me complete control over my product; I am not dependant on
suppliers who have less knowledge and/or lower standards of craftsmanship
than I do. Most parts makers (e.g. silversmiths) are not bagpipe makers,
so they don’t have knowledge of the finer points of fitting the pieces
to the pipe. Most if not all other bagpipe makers buy in at least some
of the parts for their pipes, especially the metal parts.
The most profound improvement in the drones comes from my pioneering use
of threads to fit metal parts. Prior to this idea almost all, if not all,
metal ferrules and ring caps were
drifted on, i.e. glued and hammered into
place. My method of treating the metal parts the way most of the best
makers treated ivory and art. ivory in the past, makes for much more
time in the making, but increases enormously the quality of and control
over the end product. Costwise, not only do I have to spend more time in
fitment, but I have to spend the time making the metal parts as well. Cost
and quality both go up. Because threading is so time consuming I decided to
forgo base metals, and use only silver. In 1999 the price of silver was low
enough that the cost difference between nickel and sterling was small, once
the labor cost of threading was added. The price of silver has tripled since
then, so my costs have risen as well. Because sterling silver is a very soft
metal it is difficult to cut cleanly. My experience in cutting difficult-to-machine
metals allows me to thread silver cleanly.
Visit Bagpipe Gallery >
|
 |
 |
|
 |
|
 |
Listen
to Jim McGillivray play our traditionally crafted
pipes.
|
 |
 |
|
 |
|
 |
Charley Kron, master pipe maker and Principal of C.E. Kron & Co. talks about the business of pipe making and the growing demand for quality drones and chanters in the US.
read interview > |
 |
 |
|
|